The Washington D.C. naval yard shooting put the nation on a coast to coast stun. Responders searched multiple buildings to locate the gunman. “Multiple buildings.” How many locked doors do you think that accumulates to? I’m betting the yard’s maintenance crew hadn’t offered up a humorously large ring with an assortment of keys to fumble through. This leaves ad hoc first responder teams as well as SWAT to use, shall we say, alternative tools.
But first
You need to get there. Back in 2000 Patriot3 took inspiration from an existing system and developed its Mobile Adjustable Ramp System (MARS) elevated tactics system. It had three elevated tactics systems (ETS) available—the MARS, Liberator, and RAID (Rescue, Access, Intervention and Deployment)—the connection being simply to bring you to an access point safely via a patented ramp.
The metal comes to Patriot3 cut, pieced and coated ready for assembly. Its a hard anodized aluminum capable of withstanding a wide range of environments, be that sand, salt, or snow. Over the years the weight of the system increased and Patriot3 moved to needing a straight front axle, such as the Ford F550. Popular alternatives are a Humvee or a Lenco Bearcat. The company can mount to a good number of vehicles—even cab-over-engine trucks. The weight of the MARS can run around 2,500 pounds. In comparison the Liberator is about 1,200.
Knock, knock
Now you’re at the locked door. Are you really going to kick it in or grab a screwdriver?
Roughly three years ago, Broco had the opportunity to attend an FBI breachers training event. One coordinator shared a hand-made pry bar created from the hostage rescue team—originally from a NYPD Emergency Services Unit concept. The design took a basic pry bar and glued on paracord for grip. Broco found suppliers for a cold drawn steel (hardened to 43-47 RC), a padded foam grip, as well as a 1/8-inch diameter paracord, then assembles in house: meet the Jimmy pry bar. It’s the heat-treating that pushes the Jimmy’s strength. In one test, the company took a hydraulic press to bend the 25-degree angled-end straight. It took 400 pounds of pressure, then sprang back to nearly the original angle, yet still weighs 7.5 ounces. This lightweight feature proved advantageous to one U.S. Marshal responding at the Navy-yard shooting. Reportedly the Jimmy was utilized for over 100 wooden office, as well as metal on metal, doors. The search took roughly six hours while a full-size Halligan runs roughly over five pounds.
Decades before Broco met the FBI’s homemade pry bar, their underwater exothermic torches had started being used for cutting tank track for repair—imagine the same tool on the door in your way. Exothermic torches took a fraction of time, about 30 minutes down to 6. These run about 10,000 degrees F, and a dramatically shorter pre-heat allows users to cut sooner, if not immediately. An oxygen/acetylene set runs at about 4,800 to 5,000 degrees F.
The company uses strictly oxygen. “In our case,” says Tom Joos, vice president sales and marketing at Broco, “the fuel itself is the steel-based recipe so you got metal on fire, which puts out a higher temperature.”
Using oxygen gas avoids adding additional noxious fumes, however there still could be danger in the air based on what you’re cutting. “Never use a torch to cut a hollow-core steel door, because it may have foam in it,” warns Joos. “We teach people to chase the frames instead.”
John Dapkins, owner of Jersey Tactical Corp. (JTC) had experience breaching a door or two having been on a SWAT team in New Jersey. When tools would break they’d contact the company and inform them of the problem. The typical response, he says, was “Oh, we’ll send you a new one.” Jokingly he casually says, “We don’t want another one, we want one that doesn’t break.”
They designed their Claw for a novice, or any patrol officer to be able to act without having to have had a lengthy training session. That, and with the intention of making a “tradesman’s tool,” something to last. The swing resembles an axe or sledge hammer—hold the handle at the end to maximize the physics involved. There’s a nine-pound head counter-bored onto a non-conductive handle made of a proprietary material, allowing it to flex and release energy before wrecking your hands. “Everything serves a purpose,” says Dapkins. He and his partner took four years getting the head’s angles right to create the correct leverages and points—that’s 1,000s of hours on 1,000s of real doors.
They formulated a custom mixture of over four alloys for the Claw’s head. It takes their foundry three weeks to pour to be ready for assembly.
Who’s there?
The company began development of their pole cameras in 1996. A few years later, much like the origin of the Jimmy, they encountered what Ben Kimbro, executive vice president of Tactical Electronics calls “some Frankensteined equipment” for an under-the-door camera. They took the same wireless 2.4 baseband video broadcasting technology from their PCSSs (Pole Camera Search System) and applied it to an under-the-door camera (UDC) form, the low energy frequency allowed less of a RF hazard.
Both systems are machined out of Delrin. While the company is currently in the process of ISO standardization in testing certification, Kimbro says his engineers look to exceed the required minimum standards. The cameras have been tested internally and externally to an extreme point, from throwing them across a parking lot to a 20-foot drop...“cop proof.”
At 6mm thin the UDC slips under doors, and their latest LPSS has a telescoping pole that extends to 21 feet. Prior versions had 20-inch extensions locking together. With current technology the cameras run black and white at 30 fps with the UDC at 400 lines of resolution. Pole cameras run video at 420 lines of resolution with a 0.003 lux low light rating.
From piecing together equipment to solving a technology gap, using gear from alternative markets, to creating new innovations from trial and error, innovation comes from necessity—a fact very apparent in the law enforcement world. Especially when what’s on the other side can be such a
dangerous unknown. ¦
But first
You need to get there. Patriot3, back in 2000, took inspiration from an existing system and developed its Mobile Adjustable Ramp System (MARS) elevated tactics system. With three elevated tactics systems (ETS) available—the MARS, Liberator, and RAID (Rescue, Access, Intervention and Deployment)—the connection being simply to bring you to an access point safely via a patented ramp.
The metal comes to Patriot3 cut, pieced and coated ready for assembly. Its a hard anodized aluminum capable of withstanding a wide range of environments, be that sand, salt, or snow. Over the years as the weight of the system increased and Patriot3 moved to needing a straight front axle, such as the Ford F550, popular alternatives are a Humvee or a Lenco Bearcat. The company can mount to a good number of vehicles—even cab-over-engine trucks. The weight of the MARS can run around 2,500 pounds, in comparison the Liberator is about 1,200.
Knock, knock
Now you’re at the door, the locked door. Are you really going to kick it in or grab a screwdriver?
Roughly three years ago, Broco had the opportunity to attend a FBI breachers training event. One coordinator shared a hand-made pry bar created from the hostage rescue team—originally from a concept from the NYPD Emergency Services Unit. The design took a basic pry bar and glued on a paracord for grip. Broco found suppliers for a cold drawn steel (hardened to 43-47 RC), a padded foam grip as well as a 1/8-inch diameter paracord, then assembles in house: meet the Jimmy pry bar.
It’s the heat-treating that pushes the Jimmy’s strength. In one test, the company took a hydralic press to bend the 25-degree angled-end straight. It took 400 pounds of pressure, then sprung back to nearly the original angle, yet still weighs 7.5 ounces. This lightweight feature proved advantageous to one U.S. Marshals responding at the Navy-yard shooting, reportedly the Jimmy was utilized for over 100 wooden office as well as metal on metal doors. The search took roughly six hours while a full-size Halligan runs roughly over five pounds.
Decades before Broco met the FBI’s homemade pry bar, their underwater exothermic torches had started being used for cutting tank track for repair—imagine the same tool on the door in your way. Exothermic torches took a fraction of time—about 30 minutes down to 6. These run about 10,000 degrees F, and with dramatically less of a pre-heat allows users to cut sooner, if not immediately. An oxygen/acetylene set runs at about 4,800 to 5,000 degrees F.
The company uses strictly oxygen. “In our case,” says Tom Joos, Vice President Sales and Marketing at Broco, “the fuel itself is the steel-based recipe so you got metal on fire which puts out a higher temperature.”
Using oxygen gas avoids adding additional noxious fumes, however there still could be danger in the air based on what you’re cutting. “Never use a torch to cut a hollow-core steel door, because it may have foam in it,” warns Joos. “We teach people to chase the frames instead.”
John Dapkins, owner of Jersey Tactical Corp. (JTC) had experience with breaching a door or two having been on a SWAT team in New Jersey. When tools would break they’d contact the company and inform them of the problem. The typical response, he says, was “Oh, we’ll send you a new one.” Jokingly he casually says, “We don’t want another one, we want one that doesn’t break.”
They designed their Claw for a novice, or any patrol officer to be able to act without having to have had a lengthy training session. That and an intention to make a “tradesman’s tool,” something to last. The swing resembles an axe or sledge hammer—hold the handle at the end to maximize the physics involved. There’s a nine pound head counter-bored onto a non-conductive handle made of a proprietary material allowing it to flex and release energy before wrecking your hands. “Everything serves a purpose,” says Dapkins. He and his partner took four years getting the head’s angles right to create the correct leverages and points—that’s 1,000s of hours on 1,000s of real doors.
They formulated a custom mixture of over four alloys for the Claw’s head. It takes their foundry three weeks to pour to be ready for assembly.
Who’s there?
The company began development of their pole cameras in 1996. A few years later, much like the origin of the Jimmy, they encountered what Ben Kimbro, executive vice president of Tactical Electronics calls “some Frankensteined equipment” for an under the door camera. They took the same wireless 2.4 baseband video broadcasting technology from their PCSSs (Pole Camera Search System) and applied it to an under the door camera (UDC) form, the low energy frequency allowed less of a RF hazard.
Both systems are machined out of Delrin. While the company is currently in the process of ISO standardization in testing certification, Kimbro says his engineers look to exceed the required minimum standards. The cameras have been tested internally and externally to an extreme point, from throwing them across a parking lot to a 20 foot drop—“cop proof.”
The UDC slips under doors being 6mm thin and their latest LPSS has a telescoping pole extending to 21 feet. Prior versions had 20-inch extensions locking together. With current technology the cameras run black and white at 30 fps with the UDC at 400 lines of resolution. Pole cameras run video at 420 lines of resolution with a 0.003 lux low light rating.
From piecing together equipment to solve a technology gap, using gear from alternative markets, to creating new innovations from trial and error, innovation comes from necessity—a fact very apparent in the law enforcement world. Especially when what’s on the other side can be such a dangerous unknown.
locked doors do you think that accumulates to? And I'm betting the yard's maintenance crew hadn't offered up a humorously large ring with an assortment of keys attached to fumble through. This leaves ad hoc first responder teams as well as SWAT to use, shall we say, alternative tools.
But first
From time to time officers need transport to access points, sometimes its on the ground floor, some on the second or higher. Whatever the situation Patriot3, back in 2000, took inspiration from an existing system and developed its Mobile Adjustable Ramp System (MARS) elevated tactics system. The company began work with a Chevrolet Suburban 4500 with an independent front axle. With three elevated tactics systems (ETS) available—the MARS, Liberator, and RAID (Rescue, Access, Intervention and Deployment)—the connection between them being simply to bring you to an access point safely via a patented ramp.
The metal for the ramp systems come to Patriot3 cut, pieced and coated then assembled in house. Its a hard anodized aluminum ready to withstand a wide range of environments the world can throw at it, be that sand, salt, or snow. Not wanting to drain the vehicle's power, hydraulic systems are designed to use a secondary battery. The weight of the MARS can run around 2,500 pounds, in comparison the Liberator is about 1,200. Over the years as the weight of the system increased Patriot3 moved to a straight front axle, such as the Ford F550, to allow a higher front end load rather than pushing the weight to the rear. One popular alternative is a Humvees or Lenco Bearcats, but the company can mount an ETS to a good number of vehicles—even cab-over-engine trucks.
Knock, knock
Now you're at the door, the locked door. Are you really going to kick it in or grab a screwdriver?
Roughly three years ago, Broco had the opportunity to attend a FBI breachers training event. One coordinator shared a hand-made pry bar created from the hostage rescue team - originally from a concept from the NYPD Emergency Services Unit. The design took a basic pry bar and glued paracord for grip. Staying within the U.S., Broco found suppliers for a cold drawn steel (hardened to 43-47 RC), a padded foam grip as well as the 1/8-inch diameter paracord, then assembles in house: meet the Jimmy pry bar. It's the heat-treating pushing the Jimmy's strength. In one test, the company took a hydralic press to bend the 25-degree angled end straight. It took 400 pounds of pressure, then sprung back to nearly the original angle, yet still weighs 7.5 ounces.
This lightweight feature proved advantageous to one U.S. Marshals responding at the Navy-yard shooting, reportedly the Jimmy was utilized for over 100 wooden office as well as metal on metal doors. The search took roughly six hours and a full-size Halligan runs roughly over five pounds.
Decades before Broco met the FBI's homemade pry bar, they're best known for underwater exothermic torches for commercial and Navy divers. In the late 1980s, the torches had started being used for cutting tank track for repair--imagine what the same tool would do to the door in your way. Originally, maintenance had been using oxygen and acetylene sets, the exothermic torch took a fraction -- to illustrate, what would normally take 30 minutes to cut, would take roughly 6. The torches run about 10,000 degrees F, and with dramatically less of a pre-heat which allows users to cut sooner, if not immediately. In comparison, oxygen/acetylene runs at about 4,800 to 5,000 degrees F.
1997 came the first commercial off the shelf forced entry torch set, while rods and regulators have changed slightly, the technology has remained the same for the cutting torch set. The depth of cut is a factor of diameter. The most common is 3/8-inches by 36 inches long copper-cladded steel rod with a proprietary steel-wire recipe, which should give about a two-foot long cut in a one-inch thick "mild" steel in two minutes. Broco goes up to 1/2-inch diameter as well. The company uses strictly oxygen for gas, so why such an intense degree? "In our case," says Tom Joos, Vice President Sales and Marketing at Broco, "the fuel itself is the steel-based recipe so you got metal on fire which puts out a higher temperature."
Using oxygen gas avoids adding additional noxious fumes, however there still could be danger in the air based on what you're cutting. "Never use a torch to cut a hollow-core steel door, because it may have foam in it," warns Joos. "We teach people to chase the frames instead."
John Dapkins, owner of Jersey Tactical Corp. (JTC) had experience with breaching a door or two having been on a SWAT team in New Jersey. When tools would break they'd contact the company and inform them of the problem. The typical response, says Dapkins, was "Oh, we'll send you a new one." Casually, he says "We don't want another one, we want one that doesn't break."
They designed their Claw for a novice, or any patrol officer to be able to act without having to have had a lengthy training session. That and an intention to make a "tradesman's tool," something to last. The swing resembles an axe or sledge hammer -- hold the handle at the end to maximize the physics involved. There's a nine pound head counter-bored onto a non-conductive handle made of a proprietary material allowing it to flex and release energy before wrecking your hands. The head itself includes compound angles and teeth. "Everything serves a purpose," says Dapkins. He and his partner took four years getting the angles just right to create the correct leverages and points. In that time, 1,000s of hours on 1,000s of real doors.
They formulated a custom mixture of over four alloys for the Claw's head. It takes their foundry three weeks to send it to JTC for assembly. There the handle undergoes a sprial-grind and an epoxy resin is set into the threads -- this epoxy takes 24 hours to set. Clearly JTC has no intent in rushing the production process.
Who's there?
Intelligence is key. "To be able to give a look to have some visual augmentations and some visual and spatial knowledge as to what lies beyond that door is a safety benefit," says Ben Kimbro, executive vice president of Tactical Electronics. "That is one of the shiniest examples of the fatal funnel... one, it enhances safety and two ... can control the speed of the assault."
The company began development of their pole cameras in 1996. A few years later, much like the origin of the Jimmy, they encountered what Kimbro calls "some Frankensteined equipment" for an under the door camera. At the time a solution was available, yet it kept the officer prone very near to the camera. They took the same wireless 2.4 baseband video broadcasting technology from their PCSSs (Pole Camera Search System) and applied it to an under the door camera (UDC) form, the low energy frequency allowed less of a RF hazard. Hard wired options are available.
Both systems are machined out of Delrin, this holds strength but lightweight. While the company is currently in the process of ISO standardization in testing certification, Kimbro says his engineers look to exceed the required minimum standards. The cameras have been tested internally and externally to an extreme point, from throwing them across a parking lot to a 20 foot drop -- "cop proof." He doesn't advocate using the pole camera to break a window, but it's bound to happen -- knowing police work can be rough its roughly 98% to 99% aluminum.
The company listens. Sending out systems across the country drives new designs and new innovations. While law enforcement would prefer as thin of a UDC as possible, video quality will be decrease. While officers would want a 50 foot pole camera, they'd have a tough time holding it. Currently the UDC slips under doors being 6mm thin and their latest LPSS has a telescoping pole extending to 21 feet. Prior versions had 20-inch extensions locking together. With current technology the cameras run black and white at 30 fps with the UDC at 400 lines of resolution and pole cameras at 420 lines of resolution with a 0.003 lux low light rating. A color option is available.
From piecing together equipment to solve a technology gap, using gear from alternative markets, to creating new innovations from trail and error innovation comes from necessity -- a fact very apparent in our law enforcement world. Especially in the intense situation where what's on the other side can be such a dangerous unknown.
About the Author
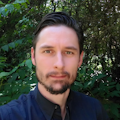
Jonathan Kozlowski
Jonathan Kozlowski was with Officer.com, Law Enforcement Technology, and Law Enforcement Product News from August 2006 to 2020.
As former Managing Editor for Officer Media Group, he brought a dedicated focus to the production of the print publications and management of the Officer.com online product and company directory. You can connect with Jonathan through LinkedIn.
Jonathan participated as a judge for the 2019 and 2020 FOLIO: Eddie & Ozzie Awards. In 2012, he received an APEX Award of Excellence in the Technology & Science Writing category for his article on unmanned aerial vehicles (UAVs) in police work, aptly titled "No Runway Needed".