Many years ago I was assigned to the Agricultural Crimes Unit with my old sheriff's department. Our unit did a lot of surveillance in rural areas using video recording systems that could be buried in the ground and left in place for weeks. The Narcotics Unit was seeing an increase in marijuana grows concealed inside orchards. My unit was asked to do a surveillance install on one of these grows. We snuck into the orchard in the middle of the night using our fancy new night vision devices (NVD). As we crept into the orchard I fell in love with my night vision. When the column came to a stop and I turned to cover our backs, I realized how unprepared I was as I had not worked out how to aim my rifle while using the NVDs. That night in the orchard I became very interested in this issue.
The Military has been using infrared (IR) aiming lasers to accurately aim infantry small arms while using night vision devices for years. They began as IR aiming lasers and have grown to the current PEQ15A which includes an IR aiming laser, visible aiming laser and IR illuminator all in one unit. Unfortunately, these devices are controlled by laws and regulations enforced by the US FDA making the acquisition of one problematic. Law enforcement and the military can purchase these higher powered units from the manufacturer, but individuals cannot. A "civilian" or commercially available IR aiming laser has been the topic of many discussions over the years. Demand has been high and has steadily increased as night vision devices become more available and higher in quality. Some agencies have been reluctant to issue higher powered IR lasers to officers because of their concern with eye safety.
This year I was blown away at the 2011 SHOT Show when I stopped in at the Laser Devices booth and struck up a conversation with Jason Clark, a junior production engineer, who was working a corner of the booth. I asked him what was new this year. The company had a new line of Class I IR lasers. What he had just said went right over my head. Clark explained that these are eye-safe and available for sale to individuals. That was when my jaw dropped. Clark took out a Class I OTAL and DBAL-I2 to show me. I ended up buying that Class I OTAL. I later learned I had purchased one of the first six Class I lasers ever produced by Laser Devices.
When I got home I arranged to put the Class I head to head with a DBAL-A2 that has a restricted Class III IR laser. Inside of buildings I could see the difference in brightness between the two IR lasers but both were effective. The difference became more apparent at about 40 yards and beyond. The brightness of the Class I dropped off while the class three remained bright. Laser Devices rates the Class I lasers to be visible out to 75 meters or 82 yards. In the urban environment of my neighborhood I was able to pick up the laser at about 100 yards, but this was dependent on what type of surface I was aiming at. Out on my parent's farm, away from street lights and such, it was easier to pick up the IR laser at distances at and just beyond 100 yards. This is not perfect, but better than nothing and is within the vast majority of law enforcement lethal force encounters.
I set up a tour with Clark to take me through the entire operation of the Laser Devices headquarters and manufacturing facility in Monterey, California. Manufacturing, testing and quality control are all housed on one floor with staff from each area interacting on a regular basis. From my perspective, it appeared that if any issues arose in the process it would be easily identified and rectified quickly with the least amount of product affected. This is a good business practice for the company and for the purchasers as a bad lot costs money and put lives at risk. Assembly of the components and the final product is done predominately by hand by skilled workers. Thermal, recoil simulation and submersion testing is done on each laser that is produced. A battery of tests is regularly completed on sample units to insure quality control including any customer requested custom testing. Clark pulled out a water exposure testing apparatus that he designed for a contract with specific requirements beyond Laser Devices extensive standard testing. Everywhere I went I saw examples of the pride that the people at Laser Devices had in the knowledge that what they made was being used by American soldiers and law enforcement officers.
At this time, the Class I lineup consists of the OTAL and ITAL Classic, EOLAD-1I and DBAL-I2 models. I asked Clark what was on the plate for the future of the Class I line. I had seen a dry erase board in the back of the office that had Class I as a header with nearly every product that Laser Devices makes written on it. Clark explained that this was just some brain storming they had been doing and that nothing was set in stone at this time. I expressed my desire to see a Class I DBAL-A2 and A3 model produced. Clark explained that at this time those units are not in the Class I lineup. He did say that if a customer wanted a Class I OTAL-A (advanced) or AR-2A he was willing to discuss it.
Clark informed me that Laser Devices is capable and willing to do custom work. While walking around the production area I had a chance to inspect some DBAL-I2 units that were being built for the military of a U.S. ally's nation. I could see that these units were set up to use AA batteries and had battery cap retention wire cables installed instead of the standard rubber lanyard. Clark stressed that customization is available to any of their customers not just large military orders. I asked him if Laser Devices could build me a AA battery version of the DBAL-I2 with a Class I laser on the right and an IR illuminator on the left in tan, but with all the control surfaces in black. His answer: "Sure. It'll be like a chocolate chip." Due to various processes in manufacturing, custom orders may take longer to deliver than standard orders, but in the end the customer gets exactly what they need.
The standard Class I DBAL-I2 has a visible red or green laser on the right side and an IR illuminator on the left. The IR illuminator can be adjusted from a wide flood to a tight beam to be used as an aiming point. The laser and illuminator are adjustable for windage and elevation. The unit can be activated by a button on top of the unit, remote pressure pad, or a constant on setting via the activation mode selector switch at the rear of the unit. The DBAL-I2 is available in models to use either a single 123 or AA battery. The AA battery units have some additional circuitry and a longer battery cap. The nice part is that by substituting a 123 battery cap on the AA model you can use 123's as well. Using AA batteries reduces battery life but allows the use of the more common AA battery. 123 units cannot use AA batteries. The DBAL-I2 is available in black or tan in both the 123 and AA versions.
Both the OTAL and DBAL-I2 come standard with Laser Devices' new HT throw lever mount. This mount appears to be superior to the mounts they previously used. The throw lever is available separately from Laser Devices if you wish to upgrade your older unit. The throw lever incorporates an attachment point for dummy cording.
I compared the current OTAL to my old OTAL and noted several design improvements including the change from a proprietary pressure pad to the US Military standard plug in type found on the PEQ-15A and the laser now projects around the left side of the unit's body. The OTAL / ITAL can be activated by the pressure pad or by rotating the activation mode selector switch to the on position. It runs on one AA battery and is very light weight and compact. The OTAL was chosen for the Class I lineup because it is one of the most popular units they offer and has been a solid and reliable performer for many years.
The EOLAD-1I mates a Laser Devices Class I IR laser to the left side of an EOTech 552 weapon sight. At the range on a cold and rainy day I put this sight through its paces. I was impressed. The optic worked great and sight in was easily done with both the optic and the laser. The weather had no affect on the laser or the optic. My main concern is that the laser and optic operate off the same batteries. If these batteries were to go dead or the battery box was damaged, both the laser and optic would be out of play. For weapons without railed hand guards the EOLAD would make a great set up. Simply attach it to a rail on top of the receiver and attach the pressure pad and you have both an IR (or visible) laser and an electronic red dot sight. After spending some time with the EOLAD I like it and want one.
The OTAL and DBAL-I2 have worked great thus far. They have held zero during shooting drills on separate M4's using rails from different manufacturers. The units have maintained zero when taking the units off and reattaching them. The DBAL-I2 I was provided for testing had a green visible laser and an IR illuminator. The illuminator is limited in range when in the flood "illuminator" settings as it is just not powerful enough to give me the range I want. When dialed into a tight beam it has worked great as an aiming point and is how I employed it during testing. My biggest concern with both designs is the adjustment knobs. The recessed knobs for the aiming laser on the DBAL-I2 appear to be superior to the ones for the OTAL Classic and for the illuminator on the DBAL-I2. The recessed version is significantly harder to inadvertently adjust out of zero versus the other types. I discussed this at length with Clark who understood my concern. We all know what can happen when a curious person wants to "check out" your gear. Some people just cannot resist turning knobs or pushing buttons. I prefer my sights not fall prey to curious hands. Using witness marks on your optics once zeroed is a smart practice, but making the act much more difficult to accomplish is a good thing as well.
Over the years Laser Devices has earned my respect as a quality and inventive manufacturer. The Class I line of IR lasers is yet another example of an American company finding creative solutions to provide an outstanding product. As the future presses on we will see the use of night vision devices in the hands of law enforcement and the need for IR aiming lasers will follow. If you have a need or just always wanted an IR aiming laser but demand quality in your kit, check out the Laser Devices line and see if one of their Class I lasers will work for you.
Dennis Haworth bio
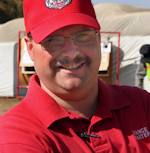
Dennis Haworth
Dennis Haworth is a police officer with a California state law enforcement agency. He has been a law enforcement range master and armorer for over a decade. He has served as a police academy instructor and has taught specialized courses on several subject matters. He has been involved in product testing for professional associations, manufacturers and law enforcement agencies. He has a BS in Criminology and an MPA with a specialization in human resources management. Much of his free time is spent as an advisor to the Shooting Sports Club at his local University of California campus.